在當今物流運輸領域,傳統的裝車方(fāng)式常常讓企(qǐ)業頭(tóu)疼不已(yǐ)。尤其是在煤炭、砂石等行業,傳統裝車的弊端(duān)愈發凸顯。
以煤炭行業為例,過(guò)去汽車裝煤大多依賴人工操作,裝車精(jīng)度宛如 “開盲盒”,欠載或超載現象屢見不鮮。工人僅憑經驗控製閘門或給煤機放煤,計量給煤機在人工頻繁啟停之下,精度大打折扣(kòu),遠不能滿(mǎn)足裝車要求。這不僅導(dǎo)致煤炭資源浪費(fèi),還可(kě)能(néng)因重(chóng)量不符引發與客戶的糾紛,給企業帶來經濟損失。而且,傳統裝車流程繁瑣複雜,司機需經曆進(jìn)場(chǎng)去皮稱重、拿提(tí)煤單、排(pái)隊(duì)裝車、交單裝煤、過磅等一係列環節,一旦裝多裝少,還得反複裝卸,極大地(dì)影響(xiǎng)了裝車效率。
再看砂石行業,傳統運輸靠人工裝卸搬(bān)運,工人肩扛手抬,勞動強度大,效率卻(què)十分低下。在(zài)忙碌的施工旺季,砂(shā)石供應常(cháng)常跟不上節奏,延誤工(gōng)程進度。同時,高強度的人工勞作伴隨著較高的安全風險,稍有不慎(shèn)就可能引發事故。
這些行業困境揭示了一個迫切的現實:傳統裝車方式人力成本高、效率低、計量精度(dù)差、安全風(fēng)險大,已難以適(shì)應現代(dài)企(qǐ)業高效、精(jīng)準、安全的發展需求。於是,汽車自動裝(zhuāng)車(chē)係統應運而生,為解決這些難題帶來了曙光。

汽車自動裝車係統猶(yóu)如一位精密的(de)智能指揮官,由多個關鍵部分協同作戰。傳感器宛如敏銳的(de) “眼睛”,負責精(jīng)準檢測貨物的位置、形狀、重量,以及車輛的型號、停放(fàng)位置等信息(xī)。常見的有激光雷達、超聲波傳感器、視覺攝像頭等,它們能在裝車現場 “洞察秋毫(háo)”。控製(zhì)器則如同智慧的 “大腦”,依(yī)據預設的裝車(chē)方案和傳感器傳來的(de)實時數據,迅速做出精準決策,計算出最佳的裝車路徑(jìng)、下料速度與位置等指令。執行機構恰似有力的 “四肢”,包(bāo)括輸送帶、機械(xiè)臂、卸料裝置等,它們接(jiē)收控製器(qì)的指令,將貨物穩穩當當地裝載到(dào)車輛上。
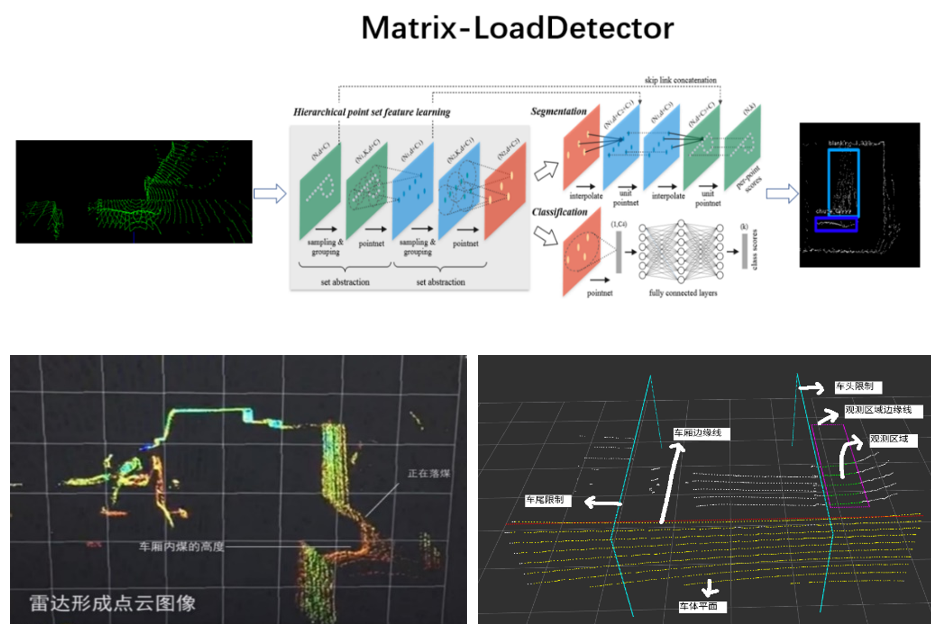
以煤炭(tàn)裝車為例,當運煤車輛緩緩駛入裝車(chē)區域(yù),地(dì)感線圈(quān)傳感器率先感應到車輛到來,隨即觸發整個係統啟動。激光雷達快速掃描車輛輪廓,確定車型、車廂尺寸及位置,將數據傳輸給控製器。控製器結合煤炭倉儲係統反饋的煤種、煤量信息,規劃裝(zhuāng)車方案,開啟(qǐ)輸送帶,煤炭經輸送帶運輸至卸料口上方的定量給煤機。定量給煤機依據指令精確控製下料量,卸料口下方的伸縮溜槽根(gēn)據車廂位置與(yǔ)料位高度動態調(diào)整角度與位置,均勻(yún)地(dì)將(jiāng)煤炭卸入車廂。裝(zhuāng)車過程中,超聲波(bō)傳感器實時監(jiān)測料位高度,一旦接近預(yù)設上限,立即反饋給控製器(qì),控製器(qì)調整下料速度或暫停(tíng)下料,防止煤炭溢出。待裝(zhuāng)車完畢,係統自動記錄裝車數據,車輛駛離,後續車輛(liàng)依序進入,重複(fù)上述流程,整個過程高效且精準。
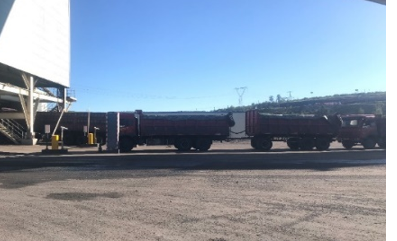
在自動裝車係(xì)統的 “智慧錦囊” 中(zhōng),先進(jìn)的傳感技術與智能算(suàn)法是兩大 “法寶”。就拿 32 線激光雷達來說,它能對裝(zhuāng)車現場環境進(jìn)行 3D 建(jiàn)模,實時捕捉車輛與貨物的動(dòng)態變化。自動裝車(chē)智能檢測算法(Matrix-LoadDetector)更是(shì)如同一位智能分析大師(shī),對激光雷達采集的點雲動態數據深入剖(pōu)析,不僅常(cháng)規的車廂邊緣、料位高度檢測不在話下,還能對溜槽位置(zhì)、車(chē)廂擋板、落料位置(zhì)等進行 AI 智能檢測,讓裝車現場的情況盡在掌握。
當車輛(liàng)駛入裝車區,激光(guāng)雷達每秒發射數百萬個激(jī)光脈衝,構建出車輛的三維模型,識別車型、車廂(xiāng)細節,如加強筋(jīn)、隔板位置(zhì)等。算(suàn)法依據這些信息,結合現場其他傳感器數據(jù),判斷車輛是否停準、下(xià)料條件是否成熟。裝車時,算法持(chí)續分析料位變化,若發現料堆形狀不均,及時指揮車輛微調位置;一旦檢測到溜槽與車(chē)廂相對位置(zhì)偏移,迅速調整溜槽角度,確保下料精準。遇到突發狀況,如車輛異常移動、物料堵塞,係統瞬間響應,關閉下料口並發出警報,全方位保障裝車安全、穩定、高效。
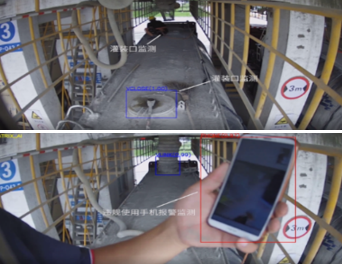
(一)高效精準,降本增(zēng)效
自動裝車係統的高效精(jīng)準令人驚歎,相較於傳統人(rén)工裝車,優勢盡顯。在某大型煤礦,過去人工裝車時,裝滿一輛載重 30 噸的運煤車,熟練工人也需近 30 分鍾,還常因計量不(bú)準返工。如今采(cǎi)用自動(dòng)裝車係統,同樣(yàng)車輛僅需 5 - 8 分鍾即可完成裝車,效率提升超 3 倍。其高精度計量係統,依托皮帶秤、定量給煤機等先進設備,裝車誤(wù)差控製在(zài)極(jí)小範圍內,有效避免超載罰款與欠載補貨,運輸成本(běn)隨之大幅(fú)降低。據(jù)統計,一家(jiā)年(nián)運輸量 100 萬噸的(de)煤礦企業,使(shǐ)用自動裝車係統後,每年因超載(zǎi)欠載減少的損失可達數十萬元,運(yùn)輸效率提升使整體運營成本降低約 15%。
(二)穩定可靠,安全(quán)無憂
穩定性與可靠性是自動裝車係統的 “硬實力”。無論是酷熱難耐的夏日,還是寒風凜冽(liè)的冬日,亦(yì)或(huò)是粉(fěn)塵彌漫(màn)的惡劣環境,它都能穩定運行。以北方某大型砂石料場為(wéi)例,冬季低溫至零下 20℃,夏(xià)季高溫超 40℃,且砂石裝卸揚塵嚴重,以往設備常故障停機。自動裝車係統采(cǎi)用耐(nài)寒耐熱、防塵密封設計(jì)的電(diàn)氣(qì)元件與機械結構,關鍵部(bù)位冗餘(yú)備份,大大減(jiǎn)少故障概率。運行多年來,平均故障停機(jī)時間較以往縮短 80%,有力(lì)保障了生產連續性。同時,係統配備多重(chóng)安全(quán)保護,如紅外光幕防碰撞、溜槽堵塞檢測、緊急製動等,一旦有異常,立即響應,全方位守護裝車安全。
(三)智能操作,便捷省力(lì)
自動裝車係統將智能(néng)化貫穿始終,操作便捷省力。在某現代化物流園區,貨物裝車涉及多種品(pǐn)類、規格,以往調度(dù)員需憑(píng)經驗安排,人工搬運裝(zhuāng)車,勞動強(qiáng)度大、效率低。如今係統依據訂單信息自動規劃裝車方案,智能調度輸送帶、機械臂等設備(bèi),少量工作人員隻需在中控室監控或現場輔助(zhù),即可輕鬆完成裝車。而(ér)且(qiě),企業主通過手機 APP 或電腦端,隨時(shí)隨地了解裝車進度、設備狀態,遠程控製啟動、暫停(tíng),實現智能化管理,人力(lì)成本降(jiàng)低約 60%,管理(lǐ)效率大幅提升。
(四)環保節能,綠色發展
在環保形勢日益嚴峻的(de)當下,自動裝車係統的環保節能特(tè)性尤為關鍵。某煤炭港口,過去煤炭露天(tiān)裝車(chē),揚塵四溢,周邊居(jū)民苦不堪言,還造成煤炭損(sǔn)耗。現采用封閉式自動裝車係統,裝車區域全封閉,配備噴(pēn)霧降(jiàng)塵、布袋除塵等裝置,揚塵汙染降低超 90%,煤炭損耗率從 3% 降至 0.5% 以內。係統還能依據車輛載重、類型,動態調整裝車速度與下料力度,避免能源浪費,契合企業可持續發展需求,為環保事業貢獻力量。